Technology & Innovation
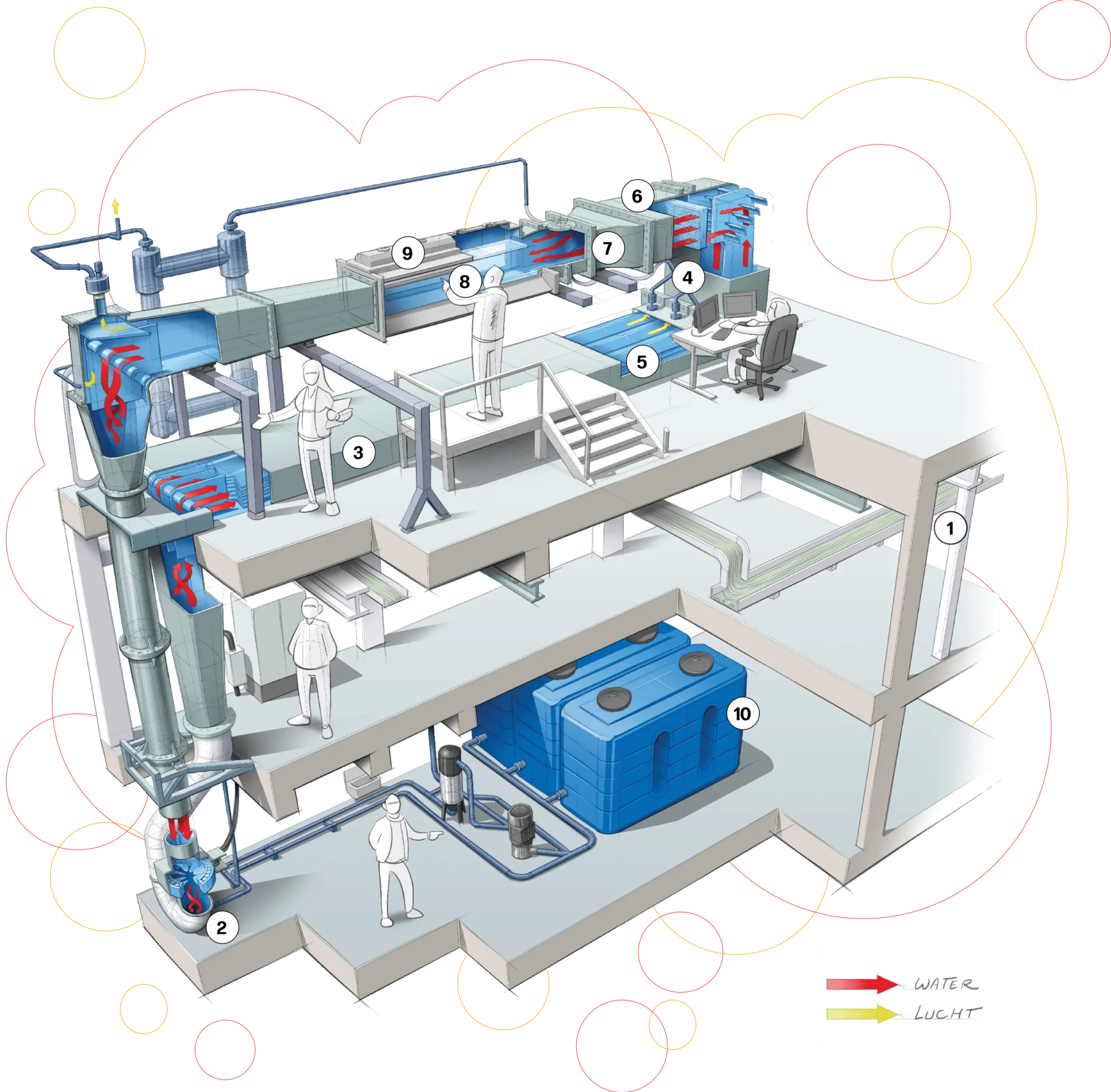

There are additional steel girders in various places to support the weight.

In the cellar, a 110-kW pump propels the water upwards.

The water then flows slowly (up to 1.56 m/s) through a wide flat box.

The box is used to capture and remove any air bubbles.

Inside, there are three sets of seven parallel roof-shaped channels to capture the bubbles.

After two sharp curves and a honeycomb for equalisation, the flow increases up to 13 m/s.

In front of the window, air can be added for air-lubrication experiments.
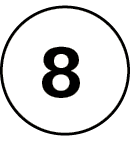
The polycarbonate windows (4 cm thick) on the front, underneath and back ensure a perfect view of the experiment.

Force transducers in the ceiling measure the friction of the flowing water.

There are storage tanks in the cellar for salt- and freshwater not in use.
© Stephan Timmers