Techniek & Innovatie Forze
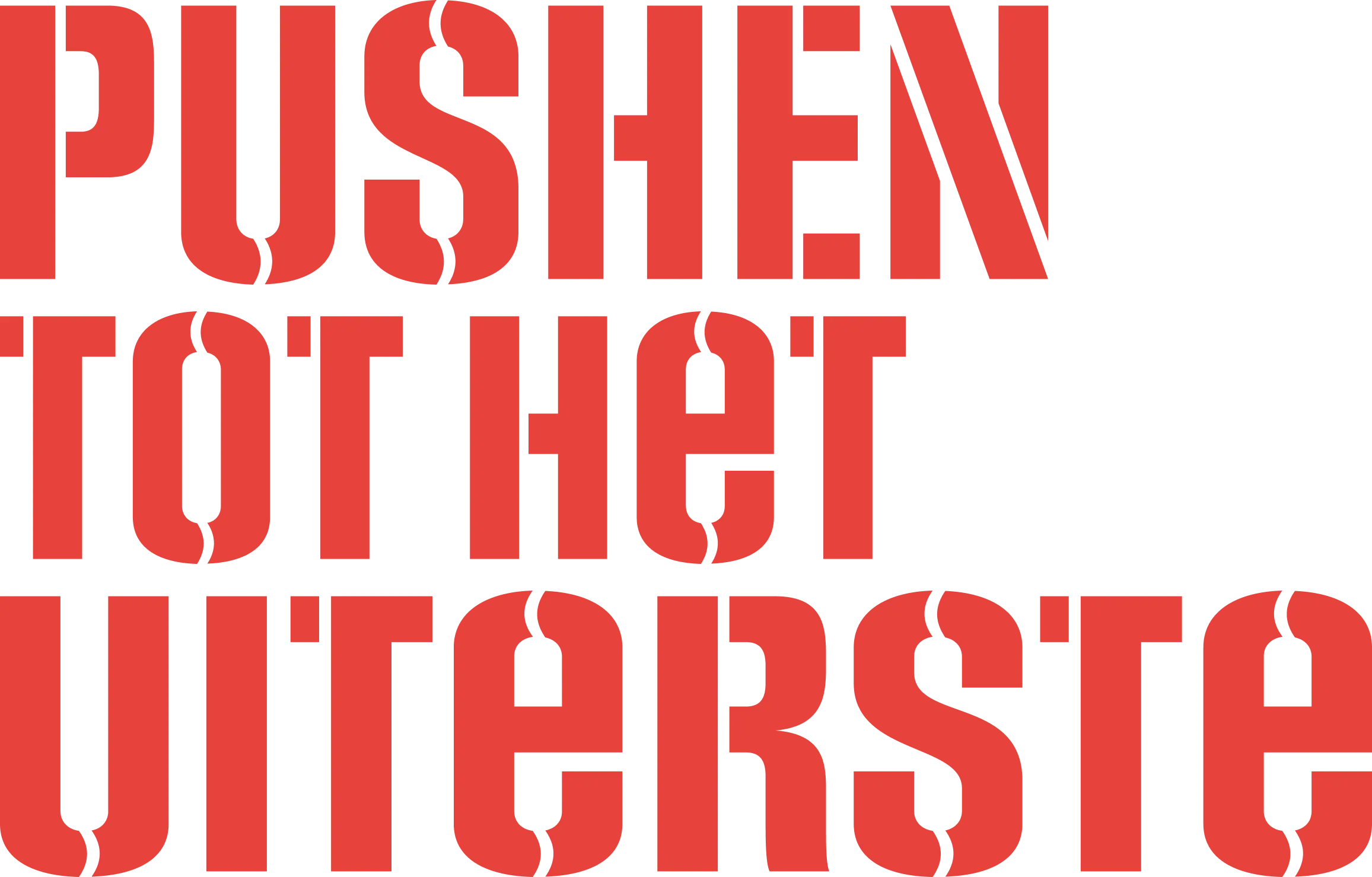

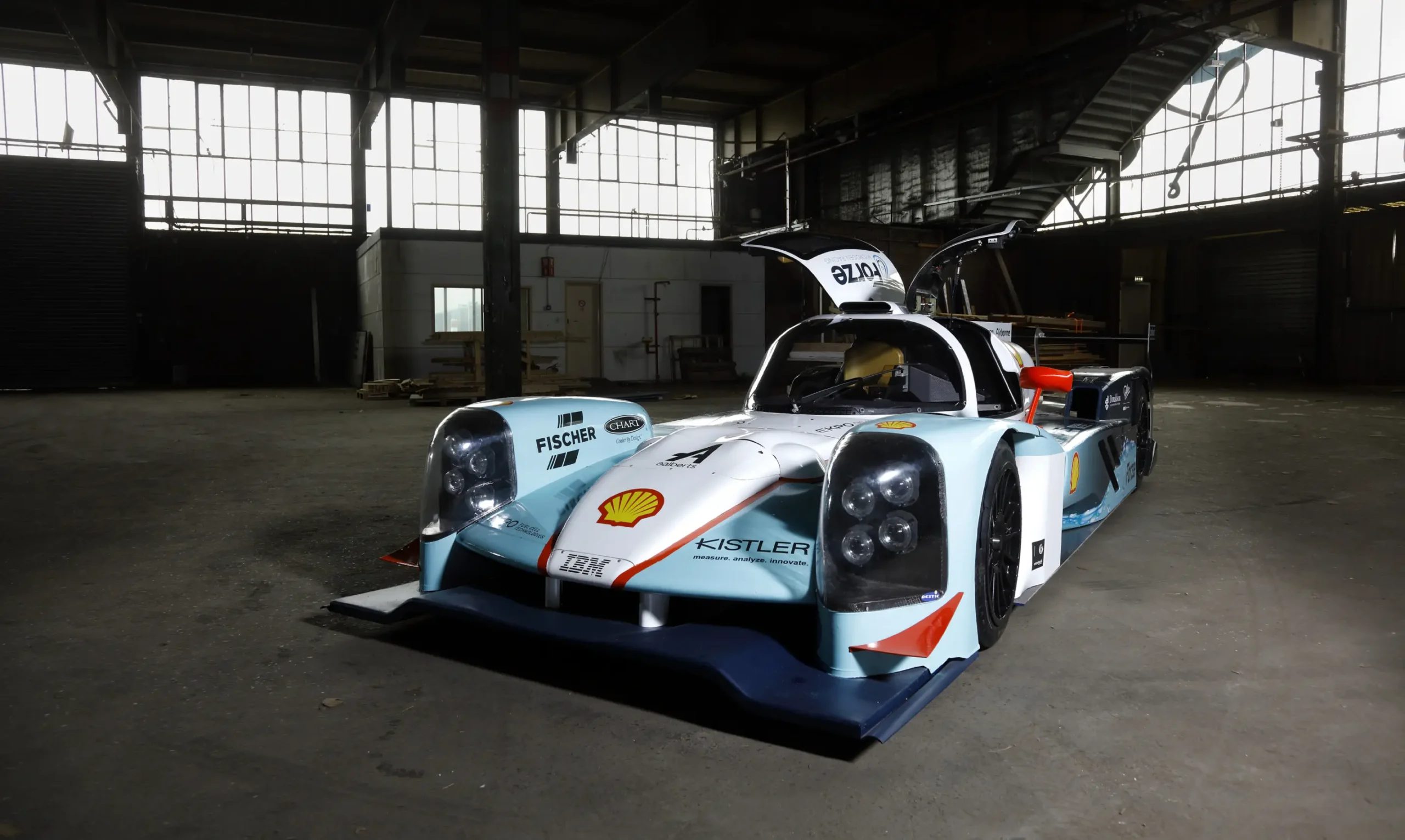
@Sam Rentmeester
Tekst Jos Wassink
In de delftste kabelfabriek werken dertig studenten samen met meer dan honderd industriële partners aan een turboracewagen op waterstof. “Dit is de toekomst van de motorsport”.
“Er zijn in de wereld maar twee racewagens op waterstof, en die staan allebei hier”, vertelt werktuigbouwkundestudent en pr-man Roel Breure in de werkplaats aan de Delftse Schieweg. “Forze IX is ontworpen om records te breken en wordt ook baanbreker voor de waterstofrevolutie.”
De historie van Forze begon in 2007. Elk jaar waren er verbeteringen en aanpassingen totdat in 2019 de beslissing viel om helemaal vanaf nul te beginnen.
“De techniek is hard vooruitgegaan”, legt Breure uit. “Onderdelen zijn kleiner geworden. Daardoor kunnen we nu twee keer meer vermogen onderbrengen in dezelfde ruimte.” De nieuwe wagen krijgt vier tanks met twee kilogram waterstof elk, goed voor een race van een uur. De wagen krijgt vierwielaandrijving met energieterugwinning bij het remmen. De brandstofcellen leveren 240 kilowatt continuvermogen.
Topsnelheid
Het piekvermogen ligt, dankzij een koffer vol met supercaps (supercondensatoren), op 600 kilowatt (800 pk). Dat moet genoeg zijn om de 1.600 kilogram zware wagen in 3 seconden van stilstand naar 100 kilometer per uur te stuwen, heeft het team berekend. De topsnelheid schatten ze op 300 kilometer per uur. Daarmee willen ze in races uitkomen tegen de top van productiewagens in de Super GT klasse.
Zover is het nog niet. Het gestroomlijnde casco staat er, maar er moet nog veel gebeuren. Alleen al voor de brandstofcel zijn er een stuk of vijf subsystemen nodig om de waterstof goed toe te voeren, en hetzelfde geldt voor de toevoervan voldoende lucht van de juiste temperatuur en vochtigheid voor de brandstofcel. Breure vertelt: “We krijgen zo langzamerhand de onderdelen binnen. Die gaan we samenbouwen en testen buiten de auto. Pas als dat goed gaat volgt de inbouw in de auto.”
Brandstofcel
De zorg voor de brandstofcel, die niet warmer mag worden dan 80 graden Celsius, bepaalt veel van het ontwerp. Zo berekende het team dat de auto op vol vermogen 190 kubieke meter lucht per minuut voor de koeling nodig heeft.
Dat is een klein formaat luchtballon in twee minuten. Maar liefst vijf koelsystemen dragen daar zorg voor.
In het verleden behoorde het Forze-team tot de erkende dreamteams van de TU Delft, met een werkplaats in de Dreamhall achter het gebouw voor Civiele techniek. De status als Dreamteam is Forze kwijt, maar dat staat de voortgang niet in de weg. In de Kabelfabriek aan de Schieweg hebben ze meer ruimte én zitten ze naast het verwante Formula Student-team dat een elektrische racewagen op batterijen bouwt.
Forze draait volledig op 120 sponsoren die kennis, componenten en geld leveren. In ruil daarvoor kunnen ze zichzelf profileren met een duurzaam project (racen op waterstof), kennismaken met gedreven technische studenten en hun prototypen testen in een raceomgeving.
“Waar anders kun je je apparatuur op vol vermogen testen tussen een loeihete elektromotor en een met ijs beslagen waterstoftank?”, vraagt Breure retorisch.
Waren vroeger de Formule-1 races de testbank voor de auto-industrie, Forze IX speelt nu diezelfde rol voor de ontwikkeling van de waterstofauto. Dat vertellen enkele sponsors (pagina 58). Naar verwachting is de nieuwste waterstofracer Forze IX volgend jaar klaar voor de start.
Turbocompressor
In een brandstofcel komen waterstof en zuurstof uit de lucht samen, en vormen elektriciteit en water. In een racewagen is dat geen kalm proces. Een compressor brengt de lucht op 4 bar druk met 130 gram per seconde. In minder dan acht seconden gaat er een kubieke meter lucht doorheen. “Zo’n compressor moet klein, krachtig en efficiënt zijn”, vertelt hoofd verkoop van Fischer Fuel Cell Compressors, Jens Krechting. De turbocharger past in een schoenendoos (15x15x25 cm), maar heeft een elektrisch vermogen van 15 kilowatt (tien stofzuigers) en drijft de compressor aan met 120 duizend toeren per minuut.
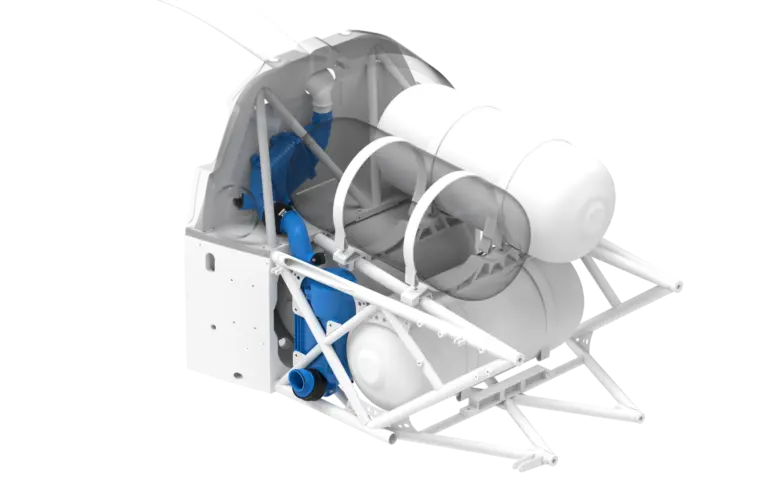
De elektromotor in het midden krijgt tot 20 tot 40 procent ondersteuning van een turbine op dezelfde as, die aangedreven wordt door het uitlaatgas van de brandstofcel. Fischer maakt compressoren voor onder meer vrachtwagens, locomotieven, schepen en de luchtvaart. Zij zien het snel wisselende vermogen van een racewagen als een interessante testomgeving. Om dezelfde reden heeft Fischer ook contact met een team dat de 24 uur van Le Mans wil doen met een waterstofauto. Een etmaal lang op vol vermogen. “Innovatie komt uit de racerij”, citeert Krechting het oude adagium in een nieuwe omgeving.
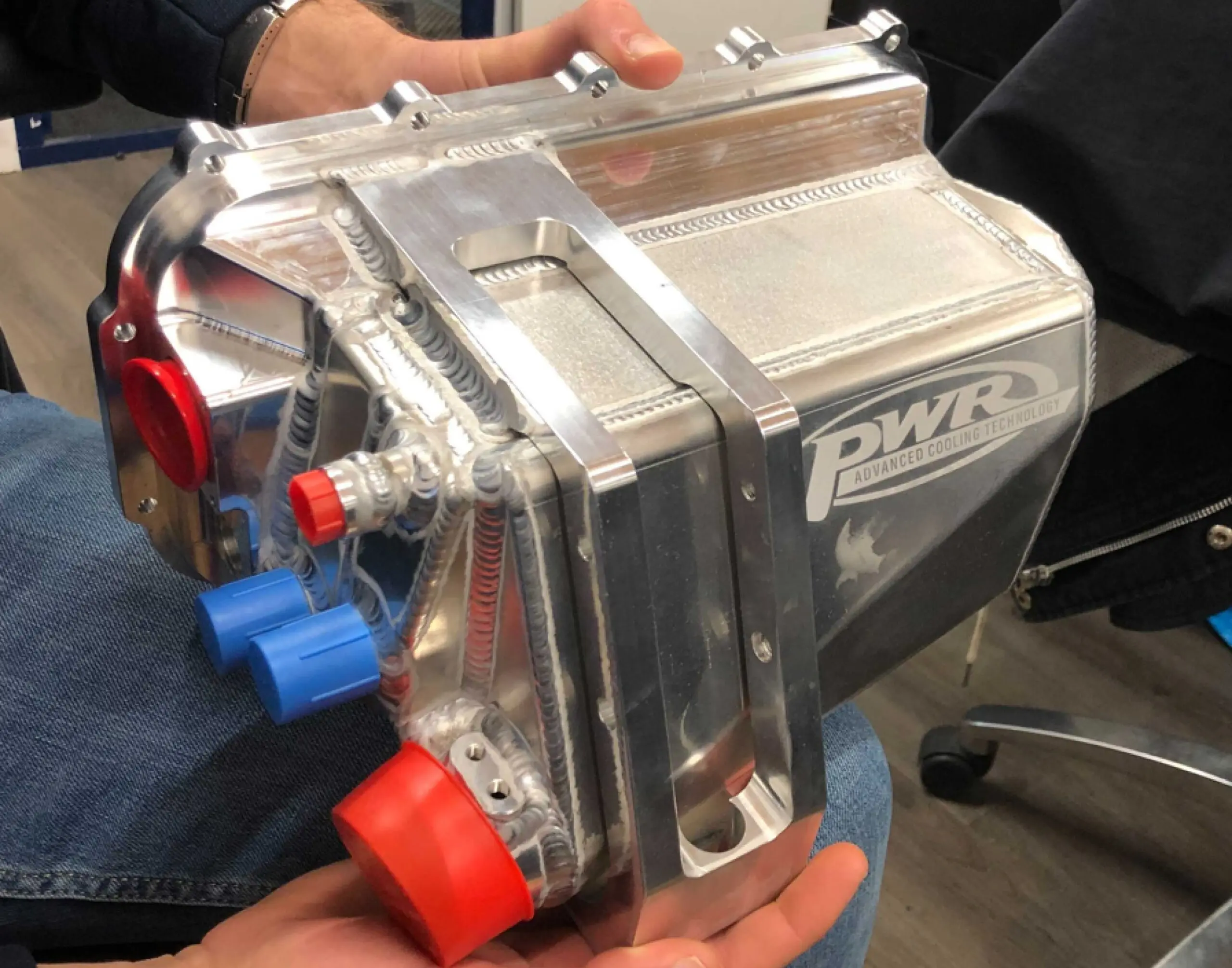
Filters
“Forze werpt een blik op wat de toekomst gaat brengen”, zegt de Belg Bart Eijkelenburg, applicatie- en ontwikkelingsingenieur bij het bedrijf Donaldson dat lucht- en vochtfilters maakt voor alles tussen oogstmachines en microsensoren. Scheiden van vocht en stof uit lucht gaat gemakkelijk als er plek is, maar bij weinig plaats en hoge snelheid wordt het topsport. En dat is precies wat Donaldson in het project Forze aanspreekt. Donaldson ontwikkelt en levert twee filters: een regenwater-, gas- en partikelfilter aan de inlaat, en een waterscheider aan de uitlaat van de brandstofcel om de turbine van de turbocompressor te beschermen.
De impact van waterdruppels bij 120 duizend toeren – je moet er niet aan denken. De filters hebben het volume van een flinke schoenendoos, maar de behuizing zal met 3D-printers aangepast moeten worden aan de beschikbare ruimte. “De turbobrandstofcel is echt next-level technologie”, vindt Eijkelenburg. “De noden en mogelijk-heden om verbrandingsmotoren nog verder te ontwikkelen worden steeds kleiner. Onze klanten hebben focus en budget om fuel cell-technologie te ontwikkelen als alternatieve energiebron. De waterstofracerij is de perfecte plaats om onze technologie naar hogere niveaus te tillen.”
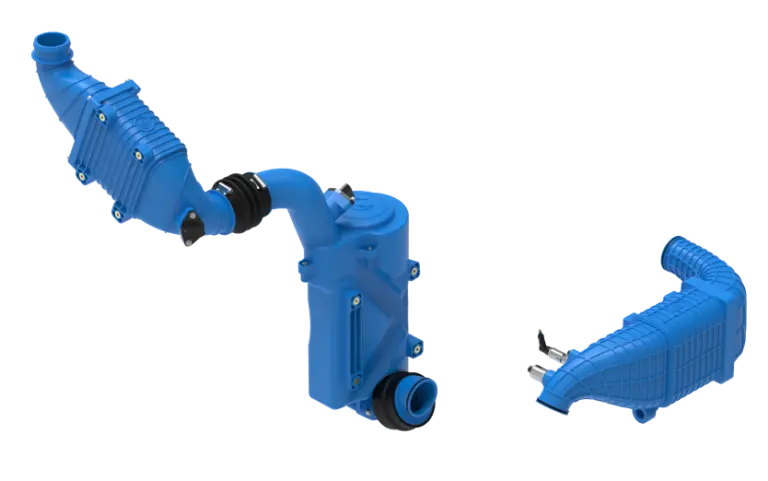
Intercooler
Hoewel afkomstig uit de turbodiesel-wereld, duikt de term intercooler ook
op bij de brandstofceltechniek. Het probleem is in grote lijnen hetzelfde: de turbo gebruikt de druk van het uitlaatgas om de lucht aan de inlaat te comprimeren. Want hoe hoger de druk, hoe meer zuurstof, hoe meer vermogen. Maar compressie verhoogt de temperatuur en maakt de lucht dunner. Daarom moet de inlaatlucht na compressie weer gekoeld worden om toch meer zuurstof naar de brandstofcel te krijgen. Dat doet de intercooler die zich tussen turbocompressor en brandstofcel bevindt.
Senior design engineer Brian Oeters van PWR in Amerika gebruikt de term charge air voor de gekoelde inlaatlucht. Die stroomt door de radiator van de intercooler, en koelt daarbij van 170 af naar 90 graden Celsius. De warmte wordt van de inlaatlucht via koelvloeistof naar de buitenlucht afgevoerd met een radiator achter op de wagen. Het hele systeem is in dubbel uitgevoerd omdat Forze twee brandstofcellen gebruikt. Oeters geniet ervan om als project engineer in dialoog met de klant oplossingen te ontwikkelen. Het valt hem op dat brandstofcelsystemen door hun lagere werktemperatuur meer koeling nodig hebben dan verbrandingsmotoren. Racewagens en vliegtuigen zijn daarom rondom omgeven met -radiatoren. Het fijne aan de samen-werking met de studenten vindt hij “de kans om uitgebreide kennis van het complete systeem te krijgen en onze berekeningen te verfijnen In tegenstelling tot bedrijfsprojecten heerst er bij de studenten openheid in plaats van geheimhouding. Studententeams zijn gewoon ‘cooler’.”
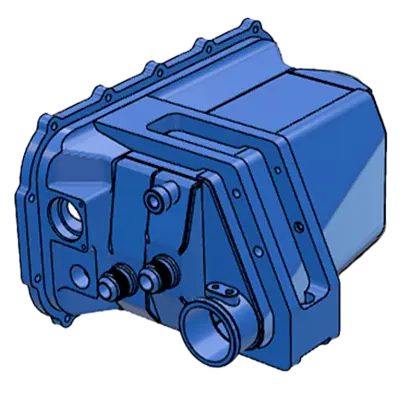