Tech & Innovation Forze
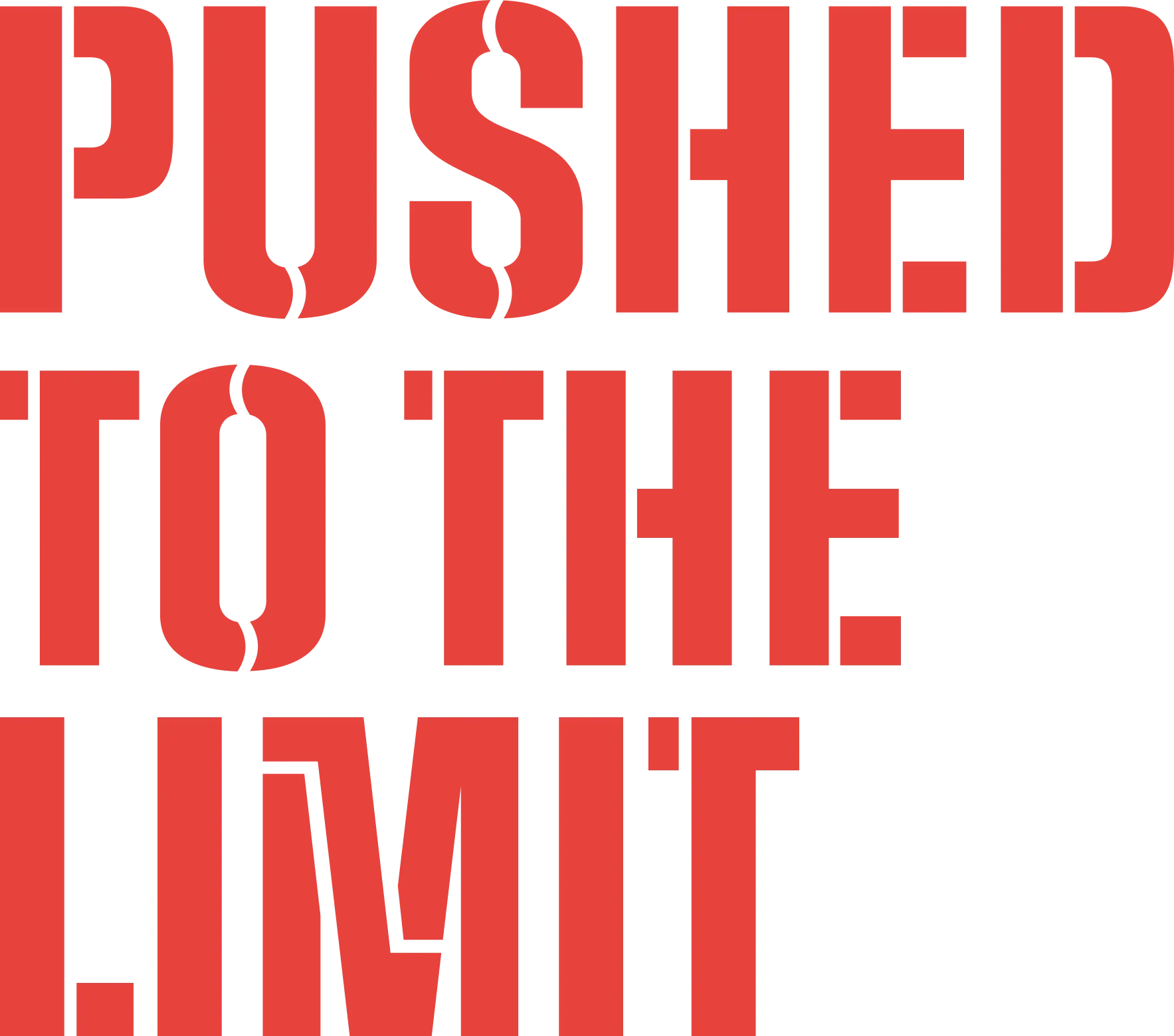

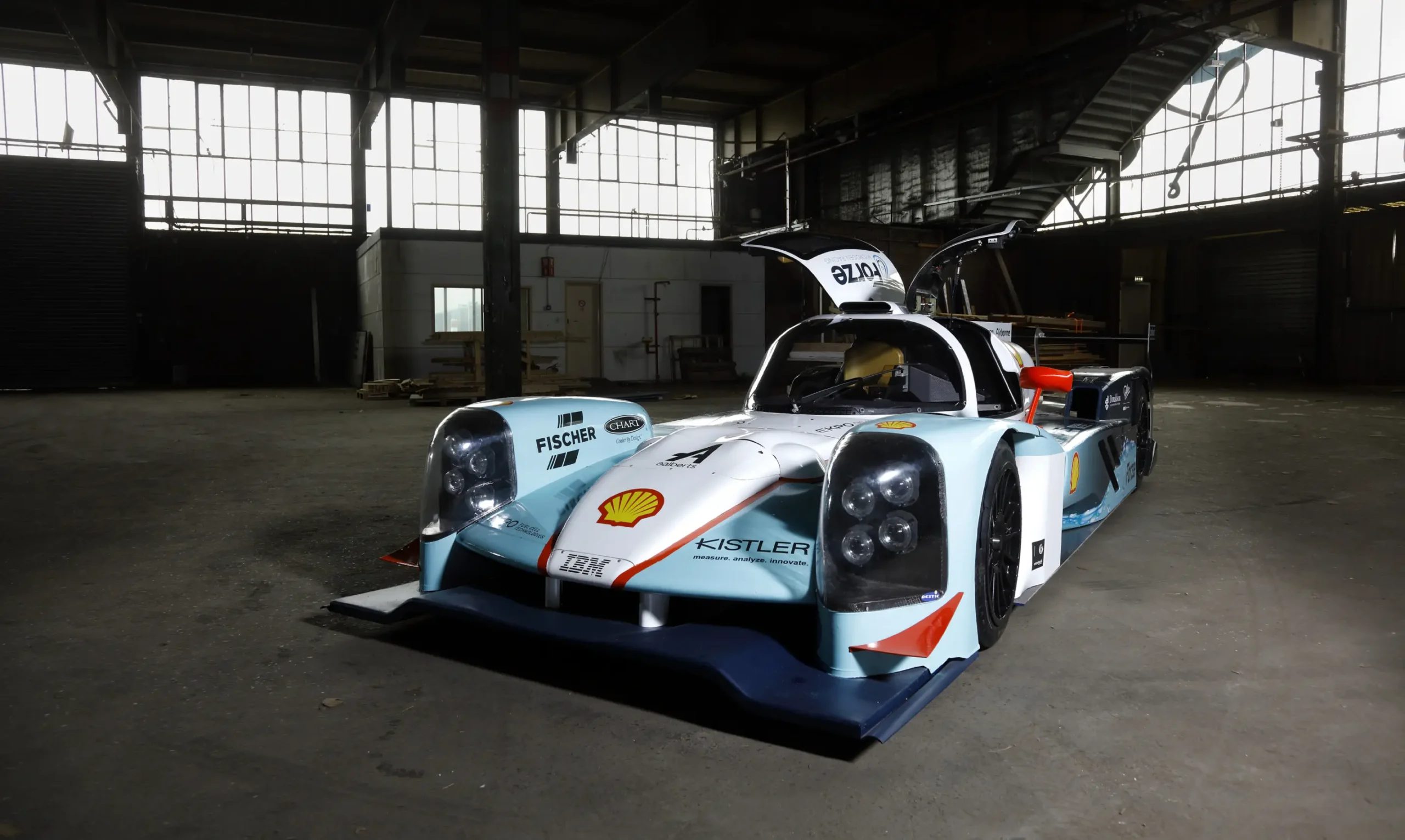
@Sam Rentmeester
Tekst Jos Wassink
In the Delft cable factory, thirty students are working woth over a hundred industrial partners on a hydrogen-powered turbo racing car. “This is the future of motorsports.”
“There are only two hydrogen-powered racing cars in the world and both of them are here”, explains mechanical engineering student and PR man Roel Breure in the workshop at Schieweg in Delft. “Forze IX was designed to break records and will be a trailblazer for the hydrogen revolution.”
Forze’s history started in 2007. There were improvements and modifications every year, until the decision was made to restart from scratch in 2019.
“The technology has progressed fast”, says Breure. “Components have become smaller. That means we can now fit twice the power in the same space.” The new car will have four tanks, each with 2 kg of hydrogen, enough for a one-hour race. The car will have four-wheel-drive and regenerative braking. The fuel cells deliver 240 kW of continuous power.
With a boot full of supercapacitators, it has a peak capacity of 600 kW (800 hp). The team worked out that that should be sufficient to enable the 1,600 kg car to reach 100 km/h from a standing stop in three seconds. The students estimate the top speed to be 300 km/h. They hope to be able to compete with the best production cars in the Super GT class.
But that is still some way off. The streamlined body is ready, but there’s still much to do. The fuel cell alone requires some five subsystems to ensure a good supply of hydrogen and the same applies to the supply of sufficient air at the right temperature and moisture for the fuel cell. Breure says: “The components are gradually arriving. We’ll put them together and test them outside the car. If that works, they’ll be integrated into the vehicle.”
Fuel cell
Concern about the fuel cell, which must not exceed 80°C in heat, determines much of the design.
The team has calculated that the car at full capacity will need 190 cubic metres of air per minute to cool it, the equivalent of a small hot air balloon in two minutes. No less than five cooling systems are needed to achieve that.
The Forze team used to be one of the TU Delft Dream Teams, with a workshop in the Dream Hall behind the Civil Engineering building. Forze has since lost its Dream Team status, but that will not hold it back. They have more space in the Cable Factory, and are based alongside the Formula Student team, now working on a battery-driven electric racing car.
Forze relies completely on its 120 sponsors who supply knowledge, components and funds. In exchange, they can associate themselves with a sustainable project (hydrogen racing), get to know passionate engineering students and test their prototypes in a race environment.
“Where else can you test your equipment at full capacity between a red-hot electric engine and an ice-covered hydrogen tank?”, asks Breure.
Where the Formula 1 races served as a testbed for the car industry in the past, Forze IX has taken on the same role in the development of the hydrogen car. This is according to several sponsors (see boxes). The latest hydrogen racer Forze IX is expected to be ready for launch next year.
Turbocompressor
In a fuel cell, hydrogen and oxygen from the air combine to form electricity and water. In a racing car, this is not a calm process. A compressor brings the air to a pressure of four bar at a rate of 130 g per second. A cubic metre of air passes through it in less than eight seconds. “The compressor needs to be small, powerful and efficient”, says head of sales at Fischer Fuel Cell Compressors, Jens Krechting. It may fit in a shoebox (15x15x25 cm), but the turbocharger has an electric capacity of 15 kW (ten vacuum cleaners) and drives the compressor at 120,000 revolutions per minute.
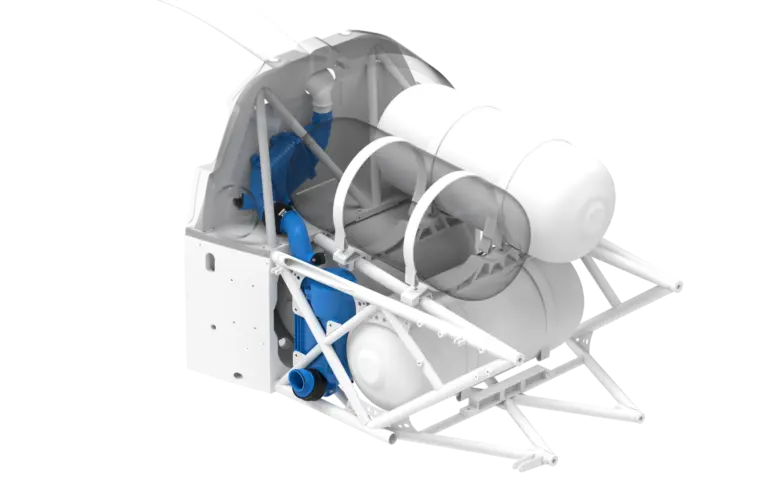
The electric engine in the middle receives 20 to 40% support from a turbine on the same axle that is driven by the exhaust gas from the fuel cell. Fischer makes compressors for trucks, locomotives, ships and aviation. For them, the fast-changing power of a racing car presents an interesting test environment. This is why Fischer is also in contact with a team that aims to race the 24 Hours of Le Mans in a hydrogen car. All day long at full capacity. “Racing is the home of innovation”, says Krechting, confirming the age-old maxim in a new setting.
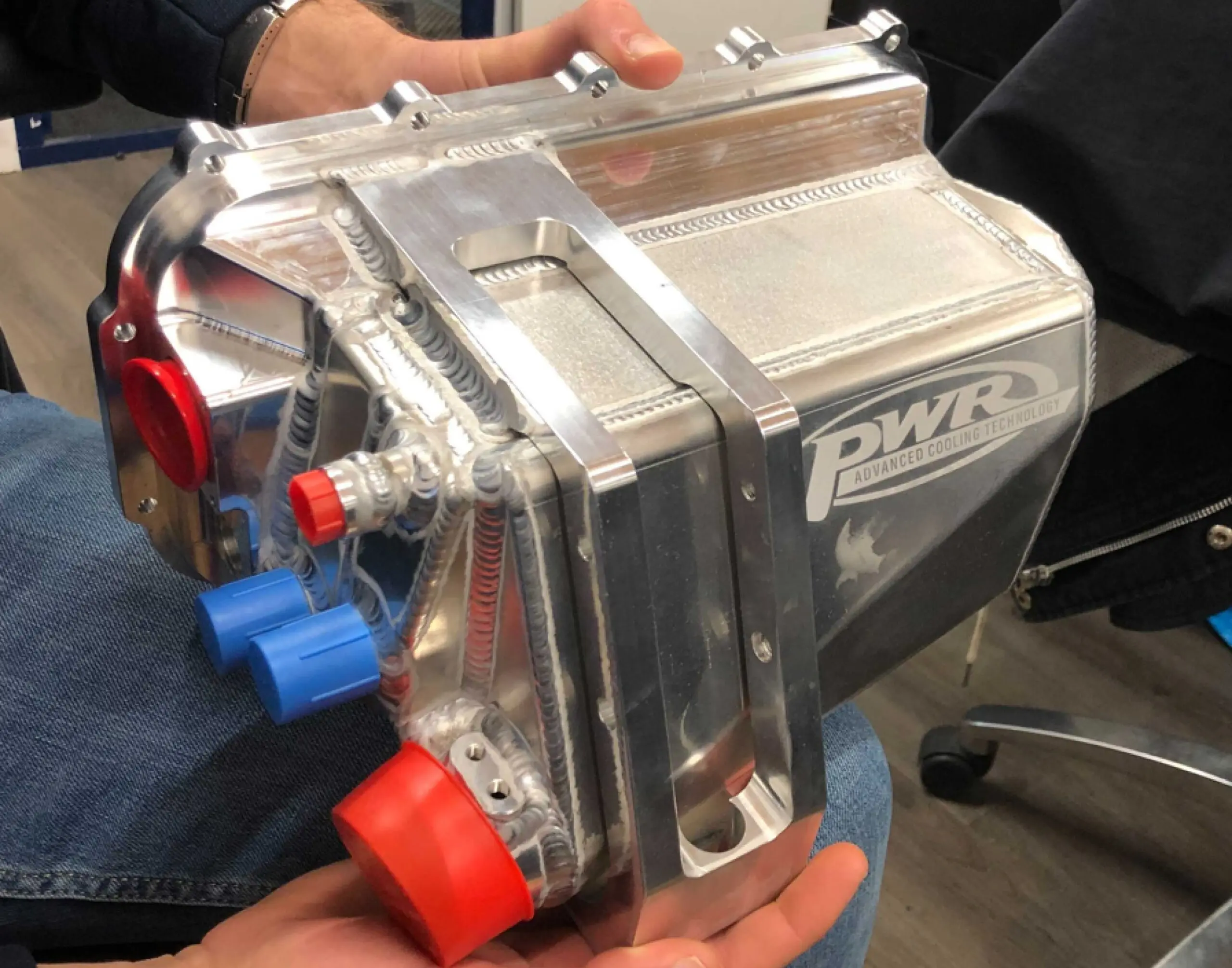
Filters
“Forze provides a glimpse of the future”, says Belgian Bart Eijkelenburg, application and development engineer at Donaldson, which makes air and moisture filters for everything from harvesters to micro-sensors. Separating moisture and dust from the air is easy if space is available, but difficult with limited space and at high speed. This is exactly what Donaldson finds appealing about the Forze project. Donaldson is developing and supplying two filters: a rainwater, gas and particle filter on the inlet, and a water separator on the fuel cell exhaust to protect the turbocompressor turbine. The impact of water droplets at 120,000 revs doesn’t bear thinking about. The filters are the size of a large shoebox, but the housing will need to be adapted to fit the available space using 3D printers. “The turbo fuel cell really is next-level technology”, says Eijkelenburg. “Combustion engine development is becoming increasingly limited. Our clients have the focus and budget to develop fuel cell technology as an alternative source of energy. Hydrogen racing is the perfect setting for raising our technology to higher levels.”
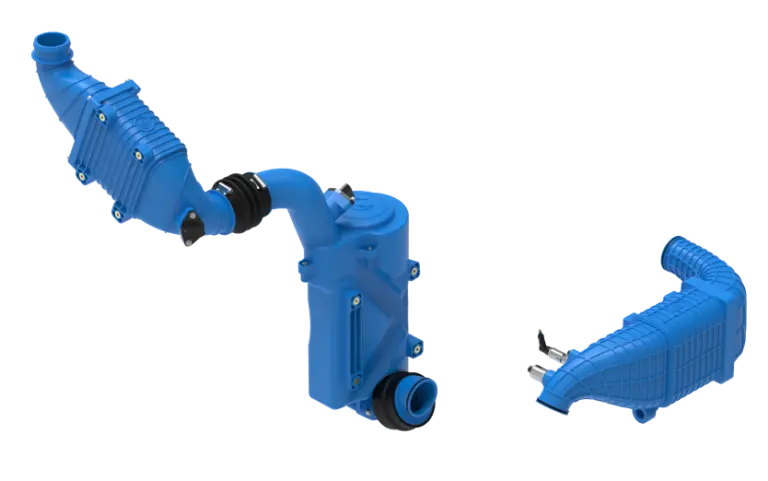
Intercooler
Although it comes from the world of turbodiesel, the term intercooler also pops up in fuel cell technology. The problem is broadly the same: the turbo uses the pressure of the exhaust gas to compress the air at the inlet. The higher the pressure, the more oxygen and the more power. But compression increases the temperature and thins the air. The inlet air therefore has to be cooled again after compression to allow more oxygen to reach the fuel cell. This is done by the intercooler, located between the turbocompressor and the fuel cell.
Senior design engineer Brian Oeters from PWR in America uses the term ‘charge air’ to describe the cooled inlet air. This flows through the intercooler radiator, cooling it from 170 to 90 degrees Celsius. The heat from the inlet air is discharged via liquid coolant to the outside air using a radiator at the rear of the vehicle. The entire system is duplicated because Forze uses two fuel cells. Oeters enjoys working as a project engineer, developing solutions in dialogue with the customer. He notes that fuel cell systems require more cooling than combustion engines because of their lower operating temperature. This is why racing cars and aircraft are surrounded by radiators. Working with students gives him “the opportunity to gain extensive knowledge of the whole system and refine our calculations. Unlike commercial projects, openness takes precedence over confidentiality here. Student teams are just ‘cooler’.”
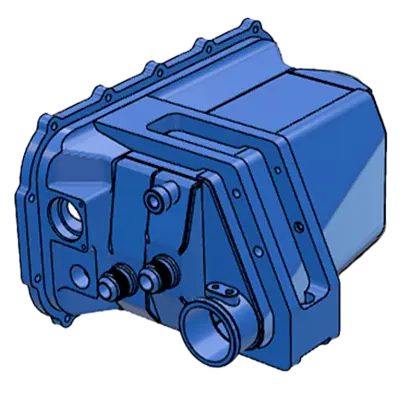